AI Predictive Maintenance Solutions
Use real-time data and machine learning to predict failures, reduce downtime, and optimize asset performance. Reduce costs and enhance efficiency with AI-driven insights tailored to your operations.
How AI predictive maintenance
works in Oil & Gas
Predictive maintenance is all about data-driven decision-making. At 7P, we gather data from two key sources: real-time machine signals and historical maintenance records. We integrate these with advanced AI algorithms to create a custom machine learning model that can detect potential issues before they become critical.
Real-Time
Data Collection
Sensors embedded in equipment transmit data to the cloud, where AI analyzes it for anomalies and potential faults. This real-time monitoring detects issues early, enabling timely maintenance.
AI-Driven
Anomaly Detection
Using advanced AI, our systems continuously monitor equipment for unusual behavior, such as deviations from normal operating parameters or signs of wear and tear. This process enables early detection of potential failures, ensuring timely interventions.
Integration with
Maintenance Records
Our system cross-references machine signals with historical data, including maintenance work orders, repair logs, and service history. This comprehensive approach enables predictive analytics, pinpointing which components are most at risk and when they are likely to fail.
GenAI for
Document Analysis
Generative AI (GenAI) plays a critical role by automatically analyzing large volumes of maintenance documents, manuals, and work orders. This allows us to enrich the AI model with contextual insights, improving the accuracy of predictions.
Challenges of traditional
maintenance approaches
Corrective Maintenance
The conventional «wait until it breaks» strategy often leads to unexpected equipment failures. This reactive approach is highly expensive due to unplanned downtime and emergency repairs.
Preventive Maintenance
Scheduled maintenance routines reduce the risk of failures, but can result in unnecessary costs by replacing or servicing components that may not need attention at the time.
Predictive Maintenance
It helps reduce costs significantly by predicting equipment failures based on data, avoiding both the overspending of preventive maintenance and the consequences of corrective maintenance.
Key Features of 7P’s Predictive Maintenance Solutions
Our AI predictive maintenance solutions are designed to
provide unmatched insights and actionable data. Key features include:
Real-Time Equipment Monitoring
Continuous analysis of machine signals from critical assets in the oil and gas industry. The system sends alerts when abnormal patterns are detected, allowing for immediate action.
Automated Maintenance Workflows
When the AI detects an impending failure, it automatically generates and prioritizes work orders, ensuring that maintenance teams focus on the most pressing issues.
Cloud Integration
Seamlessly connect your on-premise machinery to the cloud, allowing for scalable, real-time data analysis and decision-making. This setup ensures that your predictive maintenance strategy evolves with your business.
Custom AI Models
Our team creates bespoke AI models specifically for your equipment and operational needs. From drilling rigs and compressors to pumps and refinery machinery, we tailor our solutions to the specific assets in your operation.
Expertise and track record in
Artificial Intelligence and Machine Learning
When you choose 7P, you benefit from over 15 years of dedicated AI consulting excellence. Our team of AI professionals, continually educated in the latest AI and ML technologies, brings a wealth of experience to the table. Having successfully collaborated with industry leaders, we have a proven track record of delivering impactful solutions for business transformation with AI.
Years of experience
Happy customers
Successful projects
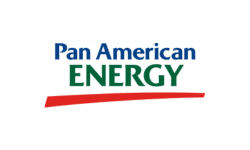
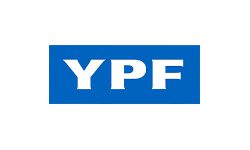
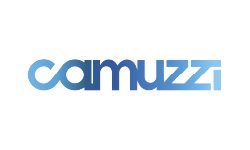
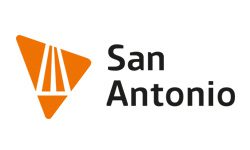
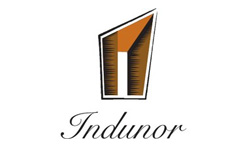
Benefits of 7P’s AI Predictive Maintenance Solutions
Cost Reduction
Avoid expensive corrective repairs and unnecessary preventive maintenance, reducing operational costs across the board.
Better Equipment Uptime
Minimizing unplanned downtime is critical, ensure your equipment stays in optimal condition, reducing disruptions and maximizing productivity.
Optimized Asset Lifespan
Ensure that each component of your machinery is maintained at the right time, prolonging its operational lifespan and reducing premature replacements.
Enhanced Safety
Early detection of faults prevents hazardous equipment failures, safeguarding your workers and the environment.
Our AI predictive maintenance solutions are designed to serve the diverse needs of the industry:
Industries and Use Cases
Upstream Operations:We help drilling companies predict the failure of drilling rigs, blowout preventers, and downhole tools, avoiding costly disruptions.
Midstream Operations: In pipeline and transport infrastructure, our solutions monitor pumps, valves, and pipelines, detecting leaks and wear before they become significant issues.
Downstream Operations: In refineries and processing plants, we ensure that complex systems like heat exchangers and compressors operate smoothly, reducing the risk of plant shutdowns.
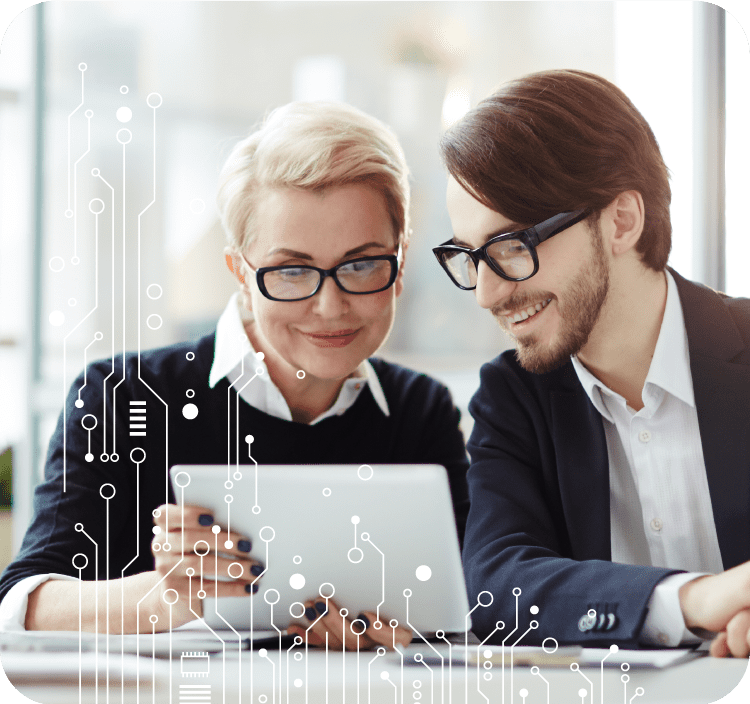
Implementing AI predictive maintenance with 7P is straightforward:
How to Get Started with 7P’s Predictive Maintenance Solutions
By integrating AI predictive maintenance into your operations, you can make smarter, data-driven decisions that keep your equipment running smoothly and your costs low. Let 7P guide you into the future of efficient, intelligent asset management.
1. Initial Consultation:
We start with a detailed assessment of your machinery, existing maintenance practices, and data sources.
2. Solution Design:
Our team develops a bespoke AI model and integrates it with your systems, providing real-time monitoring and automated predictive insights.
3. Support and Optimization:
We offer continuous support and optimization, ensuring your predictive maintenance system evolves with your operations.